Client : ENI Tunisia BV
Location : Oued ZAR-Tataouine-Tunisia
Scope of Work:
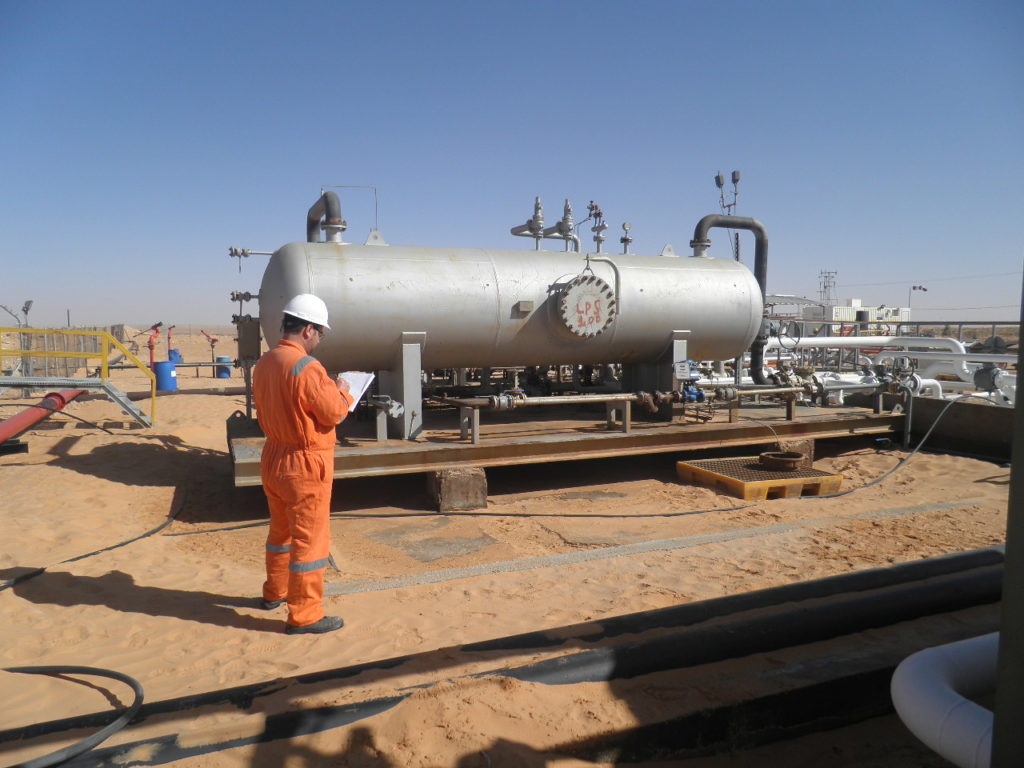
- Equipment Selection and Procurement:
- Once the grounding system design is finalized, assess the equipment required to implement the design effectively. This may include grounding electrodes, conductors, clamps, connectors, and surge protection devices. Ensure that the selected equipment complies with the ENI standards and is of high quality.
- Establish a procurement plan, including sourcing reputable suppliers or manufacturers. Consider factors like cost, lead time, and availability.
- Installation Planning: Develop a detailed installation plan that outlines how the grounding system will be implemented. This plan should include the following:
- Installation schedule and timeline.
- Responsibilities and roles of installation teams or contractors.
- Site-specific safety procedures and precautions.
- Quality control and inspection processes during installation.
- Installation & Precommissioning
- Commissioning: After successful Precommissioning, proceed with the commissioning phase. This involves testing the entire grounding system to ensure it functions as intended. Key commissioning steps include:
- Verification of the system’s resistance and impedance.
- Testing the grounding system’s effectiveness in safely dissipating fault currents.
- Measurement of touch and step potentials to ensure safety for personnel.
- Verification of proper bonding between equipment and grounding electrodes.
- Documentation
- Maintain detailed records of the entire process, including design documents, equipment specifications, installation reports, Precommissioning, and commissioning results.
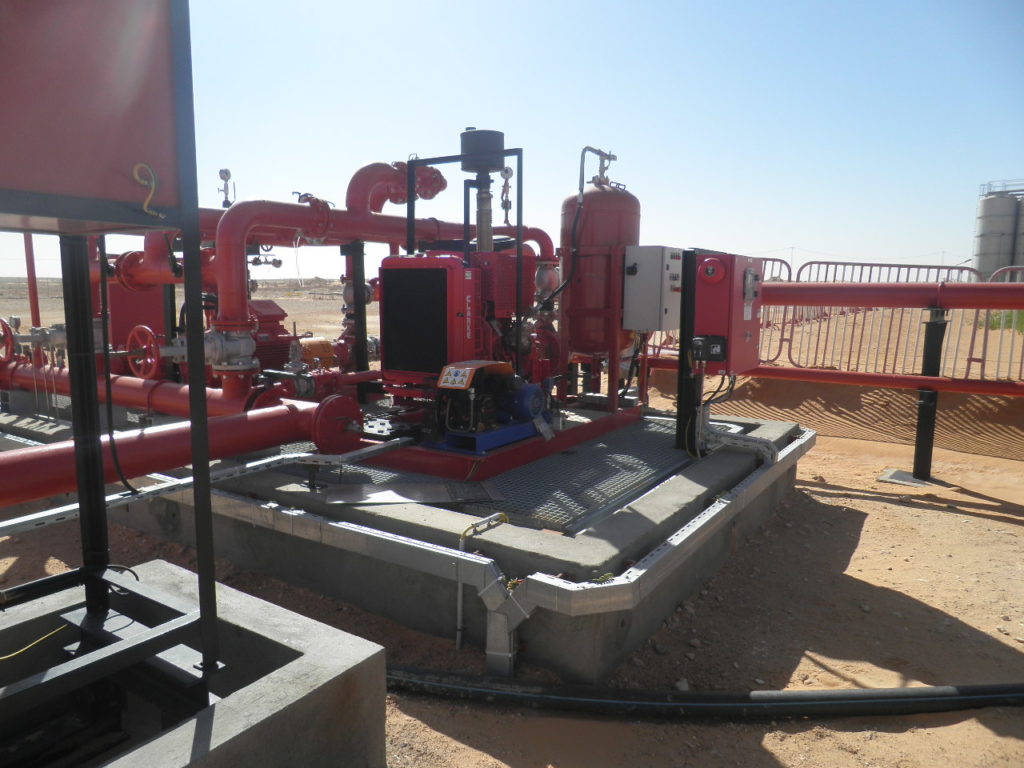